Prefab House Construction Process in India: From Factory to Site
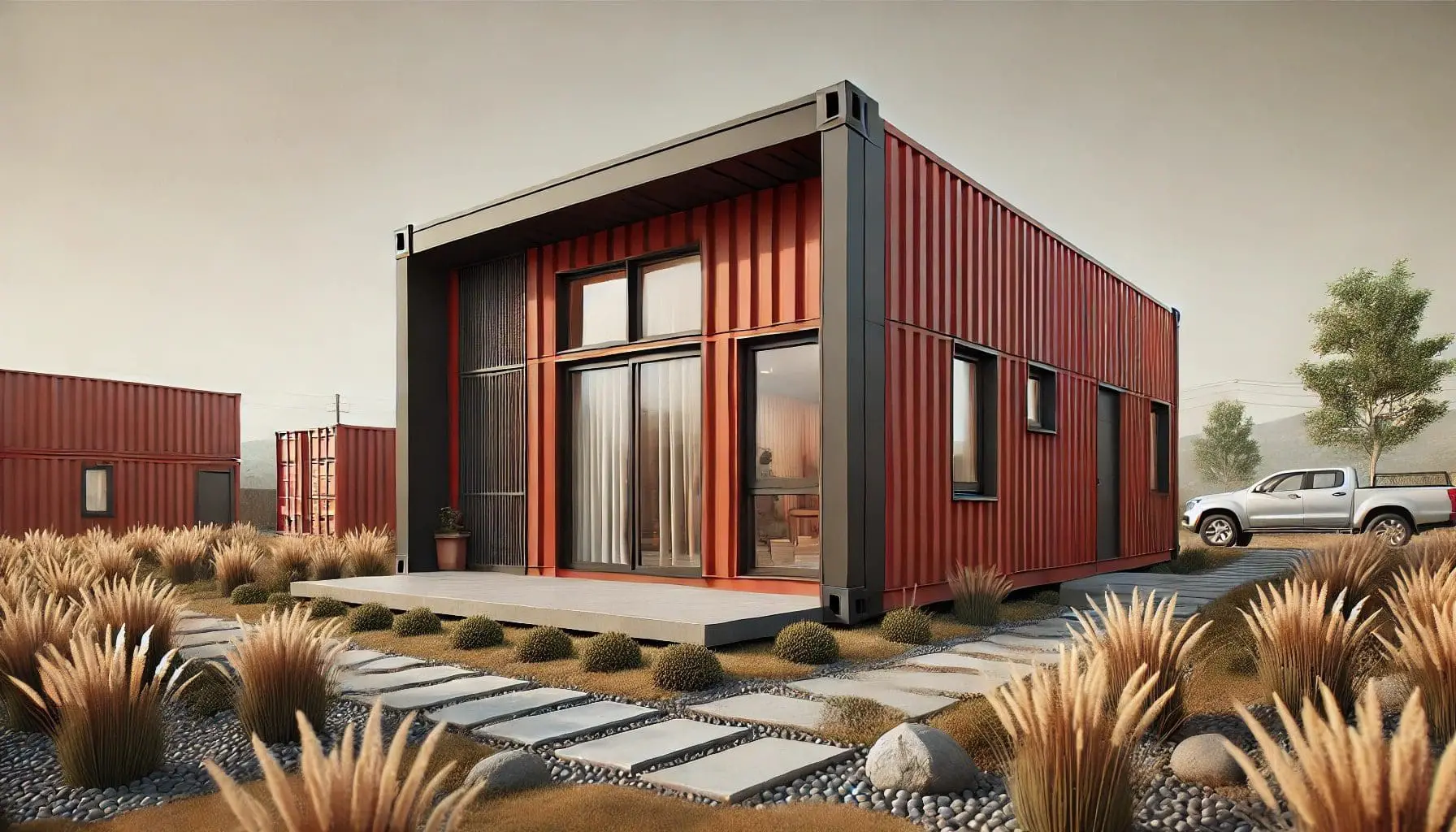
Introduction to Prefabricated House Construction
Why Prefabricated House Construction is Transforming the Industry
Prefabricated house construction has revolutionized the way homes and structures are built, offering a faster, more efficient, and cost-effective alternative to traditional construction methods. By manufacturing the main components of a home—such as walls, floors, and roofing—off-site, prefabrication reduces on-site labor, construction time, and the impact of weather on project schedules. This approach is especially beneficial in India, where rapid urbanization and housing demands call for efficient solutions that maintain high-quality standards.
The prefabricated construction process enables quick assembly and immediate usability, which is why options like modular and container homes are growing in popularity for residential and commercial needs alike. Companies such as Saman Portable provide a wide range of prefabricated solutions, from portable cabins that serve as on-site offices or temporary housing to customizable container homes that offer robust and adaptable living spaces. Each structure is built in a factory-controlled environment, ensuring consistency and high-quality craftsmanship that traditional, on-site construction may not always achieve.
For a deeper dive into modular construction, refer to Modular House India Advantages.
Benefits of the Prefab Build Method
The benefits of the prefab build method go beyond just speed and efficiency. Prefabricated house construction also promotes sustainability by minimizing material waste and reducing the carbon footprint associated with transporting materials to and from the site multiple times. Modular building approaches use fewer materials overall, and since each part of the construction is meticulously planned, there is little to no waste. Prefabricated units, like Saman Portable’s prefabricated housing options, are designed with eco-friendly practices, making them an excellent choice for those prioritizing environmental responsibility.
Explore the detailed Modular House India Advantages for an in-depth understanding of modular homes in India.
Demand for Pre-Engineered Homes in India
With the rising demand for accessible, high-quality housing in India, pre-engineered homes have become a popular option for individuals and businesses alike. These homes cater to various needs, from residential spaces to porta cabins that function as temporary offices or accommodations. As prefabrication methods advance, more people are recognizing the benefits of modular, factory-built homes for their reliability, speed, and reduced costs.
By providing cost-effective and sustainable housing solutions, prefabricated house construction addresses India’s growing need for modern, adaptable homes that fit both urban and rural landscapes. This construction method is set to become a cornerstone of the housing industry, offering practical solutions that meet the demands of a diverse population. For more about Saman Portable’s commitment to innovation in prefab construction, check their about us page.
For a faster setup option, explore Pre-built Kit Homes: Quick Affordable Housing.
Stages of Prefab House Construction in India
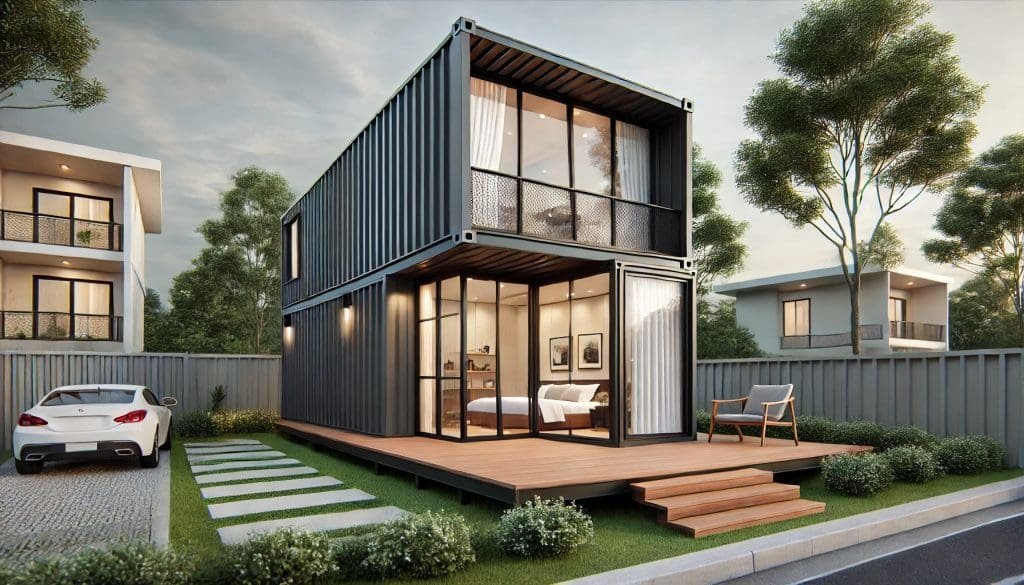
Key Stages in the Prefabricated Construction Process
The construction process for prefabricated homes in India is meticulously planned and executed across several stages, each designed to optimize efficiency, quality, and cost-effectiveness. Unlike traditional builds, where construction occurs entirely on-site, prefabricated house construction relies on a streamlined, factory-based approach that allows for greater precision and consistency. This controlled process minimizes potential delays and ensures high standards, making prefab homes an increasingly popular choice for residential and commercial applications across India. Saman Portable, a leader in modular construction, offers a range of options, including portable cabins and container-style housing, each designed to meet specific needs.
For an overview of prefabricated construction, visit Prefabricated House Construction Process.
1. Initial Design and Customization
The first stage in the prefab construction process is the design and customization phase, where clients work with designers to establish their preferences for layout, materials, and finishes. This stage is critical, as it sets the foundation for a structure that meets individual needs. For instance, clients may opt for a compact portable office cabin layout or a more spacious modular home with customized interiors. During this phase, 3D modeling and detailed blueprints allow clients to visualize the finished product, ensuring their specifications are met before manufacturing begins.
Discover Modular Housing in India Benefits for more on modular house construction phases.
2. Manufacturing and Prefabrication in a Controlled Environment
Once the design is finalized, construction moves to a factory setting, where walls, floors, and roof components are manufactured with precision. This phase ensures each module is built to exact specifications, incorporating features like insulation and wiring. The factory-based approach significantly reduces the risk of weather delays, which are common in traditional construction. Saman Portable’s prefabricated housing solutions are built in this controlled environment, resulting in durable and consistent modules that can withstand various climates across India.
3. Assembly of Modular Components and Transportation to Site
After the modules are manufactured, they are carefully assembled and prepared for transportation. Each section is equipped with features such as electrical wiring and plumbing, making on-site installation faster and more efficient. Transportation logistics are crucial, especially for larger structures like container-based homes that need specialized transport arrangements. Once the prefabricated modules arrive at the site, they are seamlessly assembled to form the complete structure, allowing for rapid installation with minimal disruption.
This step-by-step process in prefab construction enables high-quality outcomes, ensuring that each prefabricated home is built to meet industry standards and client expectations. By following these structured stages, prefabricated house construction offers a streamlined, efficient solution that meets the modern housing needs of India’s growing population.
Design Phase: Creating the Modular Blueprint
Planning and Customization in Prefab Construction
The design phase is a foundational step in the prefabricated house construction process, where every detail of the modular blueprint is meticulously planned. This stage involves close collaboration between clients and design teams to create a home that meets individual specifications and functional requirements. Clients have the freedom to customize layouts, interior finishes, and external features, ensuring their prefab home aligns with their vision. For instance, a client may want a compact portable cabin layout for temporary use or a spacious, multi-room design for permanent living. Through 3D modeling, clients can visualize the final structure, making adjustments before construction begins.
Detailed Blueprints and Model Development
Once customization is confirmed, detailed blueprints and 3D models are created, representing every structural and aesthetic element of the prefab home. This process enables clients to see a realistic representation of their finished modular home, from wall placements to room dimensions. These blueprints serve as a guide throughout the manufacturing stage, ensuring each component is crafted precisely to fit the planned layout. Whether for a container-based house or a modular office cabin, these detailed models reduce the margin for error and enhance accuracy in production.
Efficiency and Precision in Modular House Building
The design phase’s emphasis on precision benefits the entire prefab build process by ensuring each module is manufactured to exact specifications. This approach minimizes discrepancies and ensures seamless assembly when the modules arrive on-site. For larger modular buildings or specialized structures, such as portable office cabins, careful attention to detail in the design phase guarantees that utilities, insulation, and structural integrity are maintained throughout. This efficiency makes prefabricated construction particularly appealing, as it combines flexibility in design with reliability in execution.
By investing time and precision into the design phase, prefab house construction meets the growing demand in India for customizable, affordable, and efficient housing solutions. This structured approach to creating modular blueprints results in high-quality, tailored homes that cater to diverse residential and commercial needs.
Explore Modular Housing in India Benefits for customization options available in modular homes.
Manufacturing and Prefabrication of Components
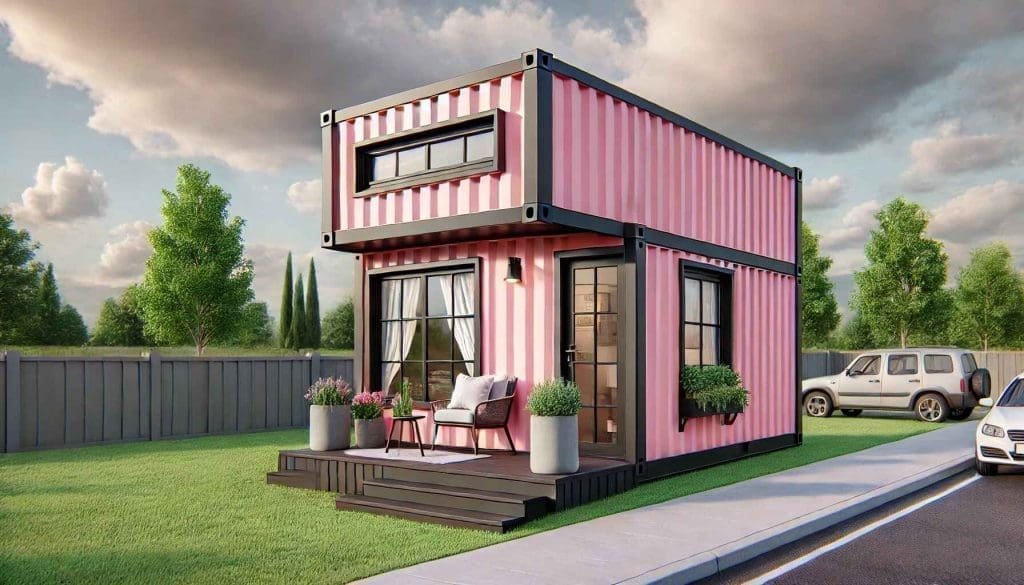
Controlled Factory Production
The manufacturing phase in prefab construction takes place in a controlled factory environment, where each component of the house is crafted with precision and quality control. This factory-based approach allows for consistent standards, as each element—walls, floors, and roofs—is produced in sections, reducing the chance of on-site construction errors. Unlike traditional building methods, prefabrication in a factory setting minimizes exposure to weather-related delays and ensures that materials are used efficiently, resulting in less waste. For clients seeking robust, durable housing solutions, options like container-based homes offer dependable prefabricated structures built to withstand varied environments.
Ensuring Quality with Modern Technology
Using advanced machinery, each module is cut, assembled, and reinforced with precise measurements. Quality checks are conducted at every step, ensuring that each component meets high durability and safety standards. Factory-based prefabrication also incorporates eco-friendly materials and energy-efficient designs, supporting sustainable construction practices. Saman Portable’s prefabricated housing options benefit from these controlled conditions, which guarantee that each unit is structurally sound and equipped with essential features, like insulation and wiring, that simplify on-site assembly.
Preparation for On-Site Assembly
During manufacturing, each module is prepared for easy assembly once transported to the final location. This includes integrating utilities like plumbing and electrical systems within the modules, so minimal work is required at the installation site. Modules for structures like portable cabins are designed with built-in features that allow them to be linked and anchored securely, ensuring they align perfectly during the assembly phase. This preparation streamlines the on-site process and reduces installation time, providing clients with a complete, functional structure that is ready for use almost immediately upon delivery.
Manufacturing and prefabrication in a factory setting are essential to the prefab house construction process, ensuring precision, sustainability, and high quality. This phase underscores why prefabricated homes are gaining traction in India, as they provide consistent, dependable housing solutions built to last. By following a structured, controlled manufacturing process, prefab homes meet the demands of India’s rapidly growing housing market efficiently and reliably.
Assembly and Transportation of Modules
Bringing Prefab Modules Together for Final Assembly
After each module is manufactured in a controlled factory environment, the next stage is to assemble and prepare the modules for transport to the designated site. This phase requires careful attention to ensure that each prefabricated component aligns perfectly upon arrival. Modules are pre-fitted with essential features, such as electrical wiring and plumbing, making the final on-site assembly faster and more efficient. Whether for a container-based home or a modular office, the modules are inspected to ensure that all components are ready for quick and seamless installation.
Logistics and Transportation to the Construction Site
The transportation of prefab modules requires meticulous planning, particularly for larger structures. Each module is carefully loaded and secured to minimize any movement or damage during transit. Special equipment and transport vehicles are used to carry the modules safely to the site, especially when dealing with large units like portable cabins or other extensive prefabricated structures. Saman Portable ensures that transportation logistics are managed efficiently, allowing modules to arrive intact and ready for assembly, even in remote or challenging locations.
Efficient and Seamless On-Site Assembly
Once the modules arrive on-site, they are positioned and anchored according to the pre-approved blueprint, allowing for a rapid assembly process. Modules are connected, bolted, and sealed, creating a stable and cohesive structure that aligns perfectly with the planned layout. This efficiency is particularly valuable in projects requiring quick setups, such as porta cabins for temporary accommodations. With the pre-installed utilities and modular design, final assembly on-site is completed within days, minimizing disruptions and enabling immediate occupancy.
The assembly and transportation phase highlights the logistical efficiency of prefab house construction, demonstrating how prefabricated homes provide a convenient and streamlined solution to modern housing needs. By focusing on precision, quality control, and efficient logistics, this stage ensures that modular homes meet both residential and commercial requirements with ease.
Learn about the speed and affordability of Pre-built Kit Homes: Quick Affordable Housing.
On-Site Installation and Assembly
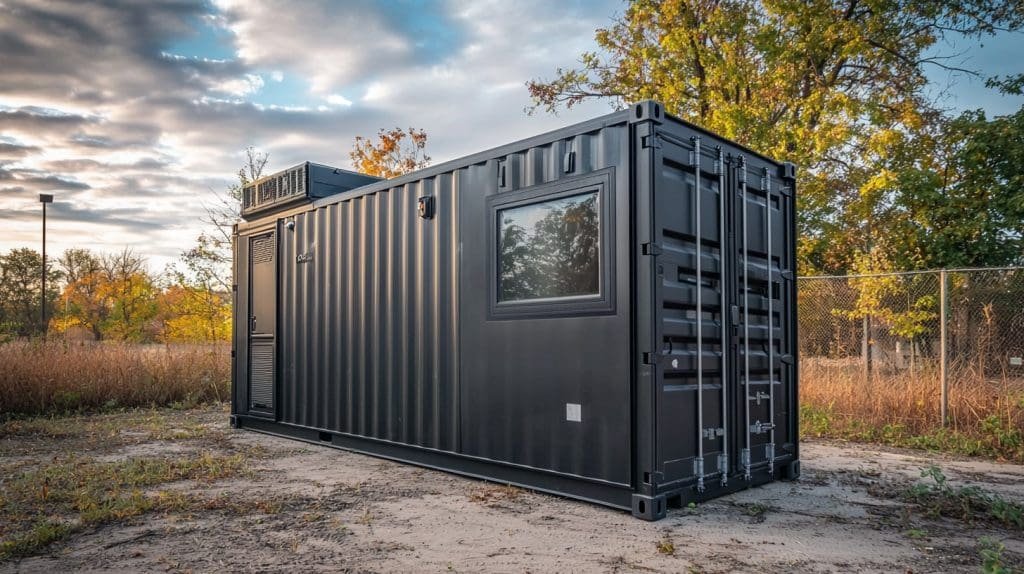
Final Assembly and Module Connection
The on-site installation phase is where the prefabricated modules come together to form a complete structure. Each module is positioned based on the layout established in the design phase, and the final assembly begins. During this stage, modules are connected, bolted, and aligned to ensure a cohesive, structurally sound building. This process is efficient and streamlined, allowing even large modular setups, such as portable office cabins, to be fully installed within a short timeframe. The on-site assembly minimizes labor time and reduces potential disruptions, which is particularly beneficial for commercial and residential projects requiring quick occupancy.
Precision and Quality Assurance in Final Assembly
At this stage, each module undergoes thorough inspection to ensure the quality and stability of the connections. Precision is critical, as proper alignment and secure bolting between modules are essential for a stable, long-lasting structure. Saman Portable’s prefabricated homes follow strict quality control protocols, ensuring that each connection is secure and every module aligns perfectly with the rest. This high level of quality assurance during the on-site assembly process guarantees that the structure meets durability and safety standards.
Minimizing On-Site Disruptions for Quick Occupancy
One of the significant advantages of prefab house construction is the minimal on-site disruption. Since each module arrives pre-fitted with essentials like wiring, plumbing, and insulation, installation requires far less time compared to traditional builds. For larger projects, such as container-based housing, the quick assembly and efficient setup make prefab construction a practical choice, especially in busy or high-demand locations. The reduced labor requirements and shorter construction period allow homeowners or businesses to occupy the space promptly, making modular housing a versatile solution for various needs.
The on-site installation and assembly process completes the transition from modular components to a fully functional structure. This stage underscores the efficiency of prefabricated construction, offering a reliable, high-quality solution that meets the growing demands for modern housing in India.
Integration of Utilities and Final Finishes
Setting Up Electrical and Plumbing Systems
In the integration phase of prefab house construction, utilities like electrical wiring and plumbing are finalized to ensure the structure is fully functional. While most of the electrical and plumbing systems are pre-installed within the modules during the manufacturing stage, final connections and checks are completed on-site to confirm everything operates smoothly. For structures such as portable office cabins or modular homes, this stage ensures that lighting, outlets, and water systems are seamlessly integrated, making the building ready for immediate occupancy.
Interior and Exterior Finishes for Aesthetic Appeal
Once utilities are in place, the next step is to apply interior and exterior finishes that give the prefab house a polished, completed look. Interior finishes can include painting, flooring, and cabinetry installation, all customized to match the client’s design preferences. Exteriors may be clad with materials such as wood, metal, or composite to enhance durability and aesthetic appeal. Saman Portable’s container homes and prefab units come with customizable options for both interiors and exteriors, allowing clients to personalize their space while maintaining durability.
Ensuring Quality Through Final Inspections
As the finishing touches are completed, a thorough inspection is conducted to ensure that every aspect of the structure meets quality and safety standards. This final inspection checks the integrity of utility connections, the stability of fixtures, and the overall aesthetics, ensuring that the prefab home is built to last. Saman Portable’s prefabricated housing options undergo rigorous quality checks to ensure that each element meets high standards, providing clients with peace of mind about their investment.
The integration of utilities and final finishes completes the prefab house construction process, delivering a move-in ready space tailored to individual needs. This efficient, high-quality approach makes prefabricated homes an appealing solution for both residential and commercial spaces in India, meeting modern demands for functionality and aesthetics.
Quality Checks and Safety Inspections
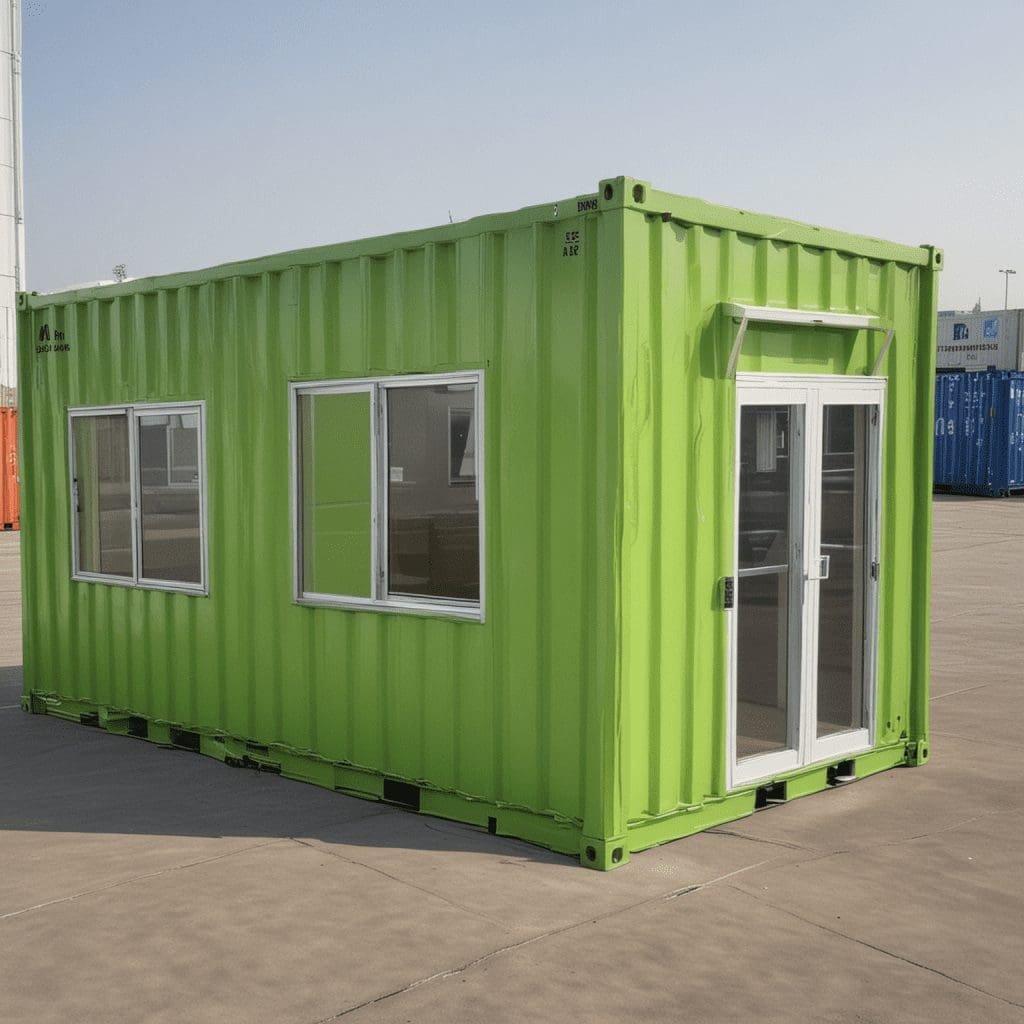
Comprehensive Inspection Protocols
The final phase in prefab house construction is a thorough quality and safety inspection to ensure that each structure meets high standards for durability, safety, and functionality. Quality checks are conducted on all aspects, from structural stability to finishing details, verifying that every part of the prefab home aligns with client expectations and regulatory guidelines. This inspection includes checking module connections, stability of installed fixtures, and seamless integration of utilities, such as electrical and plumbing systems. Saman Portable’s portable cabins undergo rigorous testing, ensuring a safe, reliable, and ready-to-use space upon delivery.
Ensuring Compliance with Safety Standards
Prefabricated house construction in India must comply with regional and national building codes and safety standards, particularly when intended for permanent occupancy. Each prefab unit, including Saman Portable’s container homes, is built to meet industry standards for wind resistance, seismic stability, and fire safety. This ensures that the modular homes are resilient and able to withstand diverse environmental conditions, making them a safe housing option across different regions in India.
Final Walkthrough and Client Approval
Once all safety and quality checks are completed, a final walkthrough allows clients to review their new prefab home and verify that it meets their requirements. This walkthrough serves as a last check for clients to inspect finishes, layouts, and any custom features, ensuring complete satisfaction before occupancy. Saman Portable prioritizes client input throughout the construction process, from design to final approval, making prefabricated homes a reliable choice for customizable, high-quality living and working spaces.
These rigorous quality checks and inspections ensure that prefab homes meet safety standards, providing reliable and secure housing solutions. By focusing on thorough inspection protocols, prefabricated house construction delivers long-lasting, high-quality results that stand up to the demands of modern living.
Cost Efficiency and Environmental Benefits of Prefab Build
Lower Construction Costs and Reduced Waste
Prefabricated homes are highly cost-effective due to their streamlined construction process and efficient use of materials. Unlike traditional builds, which often incur unforeseen expenses and delays, prefab house construction is meticulously planned, reducing the likelihood of budget overruns. The factory-controlled environment allows for precise material use, minimizing waste and lowering costs. This efficiency benefits homeowners and businesses alike, as options like Saman Portable’s prefabricated housing solutions offer affordable and durable structures without compromising on quality.
Sustainable Building Practices and Eco-Friendly Materials
One of the core advantages of prefabricated homes is their contribution to sustainability. The factory-based process reduces on-site disruptions and environmental impact, as materials are used more judiciously and construction waste is minimized. Many prefab homes incorporate eco-friendly materials, such as recycled metals and energy-efficient insulation, which support sustainable building practices. Saman Portable’s container-style homes exemplify this approach, combining environmentally responsible materials with energy-saving designs to reduce the home’s overall carbon footprint.
Find out more about sustainable options in our Readymade Houses in India Benefits guide.
Energy Efficiency and Long-Term Savings
Prefab homes are designed with energy efficiency in mind, incorporating features like high-quality insulation, double-glazed windows, and ventilation systems that help reduce energy consumption. This focus on energy efficiency not only lowers utility costs but also reduces greenhouse gas emissions, supporting a greener lifestyle. Saman Portable’s portable cabins and other prefab options can be customized with sustainable features, providing long-term savings for homeowners and businesses looking to reduce their environmental impact.
By offering cost-effective, eco-friendly, and energy-efficient building solutions, prefab homes present a practical alternative to traditional construction. The economic and environmental benefits of prefabricated homes make them an ideal choice for individuals and organizations seeking sustainable, high-quality housing solutions that align with modern values and priorities.
Visit Prefabricated House in India Benefits to see how prebuilt houses stand the test of time.
Future of Prefab House Construction in India
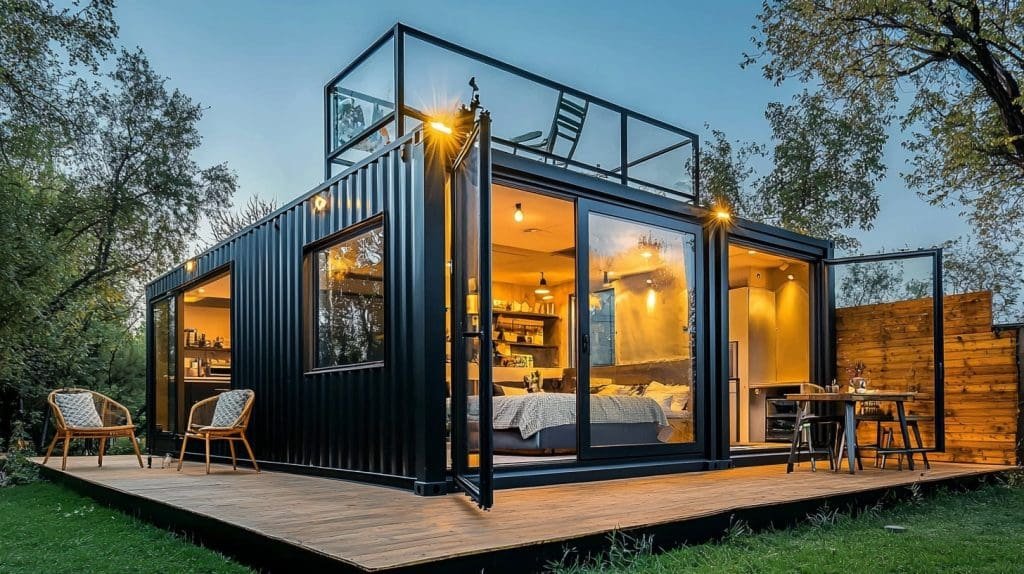
Emerging Trends and Technological Advancements
As the demand for sustainable, affordable housing continues to grow in India, the future of prefab house construction is set to evolve with new technologies and design innovations. Advanced manufacturing techniques, such as 3D printing and robotic assembly, are expected to streamline the production process further, reducing costs and construction times. These advancements enable modular housing to meet the diverse needs of urban and rural populations across India more efficiently. Saman Portable is at the forefront of adopting new technologies, developing cutting-edge prefabricated housing solutions that align with future housing trends.
Sustainability and the Rise of Green Prefab Homes
Sustainability will play a significant role in the future of prefab construction. Eco-friendly materials, energy-efficient features, and sustainable practices are increasingly becoming standard in prefab homes, aligning with India’s environmental goals. Modular homes are expected to incorporate features like solar panels, rainwater harvesting systems, and smart climate controls, which enhance energy savings and reduce the overall environmental footprint. Products like container-based housing offered by Saman Portable showcase these environmentally conscious designs, providing clients with homes that are both functional and eco-friendly.
Learn about sustainable living options in Readymade Houses in India Benefits.
Modular Homes as a Solution for India’s Housing Shortage
With India’s rapid urbanization, modular homes present a viable solution to the country’s housing shortage, offering quick-to-build, high-quality homes that meet both residential and commercial needs. Prefab housing can be deployed in a fraction of the time required for traditional builds, allowing for immediate occupancy in high-demand areas. This scalability makes modular homes an ideal choice for urban centers, rural developments, and disaster-relief housing alike. Saman Portable’s portable cabins and other modular structures are designed to adapt to diverse uses, from temporary accommodations to permanent residences.
As India moves toward sustainable development, prefab housing is positioned to play an integral role in meeting the country’s evolving needs. The combination of technological advancements, sustainable building practices, and the versatility of modular design promises a bright future for prefab house construction in India, making it a key component of the country’s housing landscape. For more about Saman Portable’s commitment to innovation in prefab housing, visit their about us page.