PEB Building Cost: Affordable, Durable, and Sustainable Construction Solutions
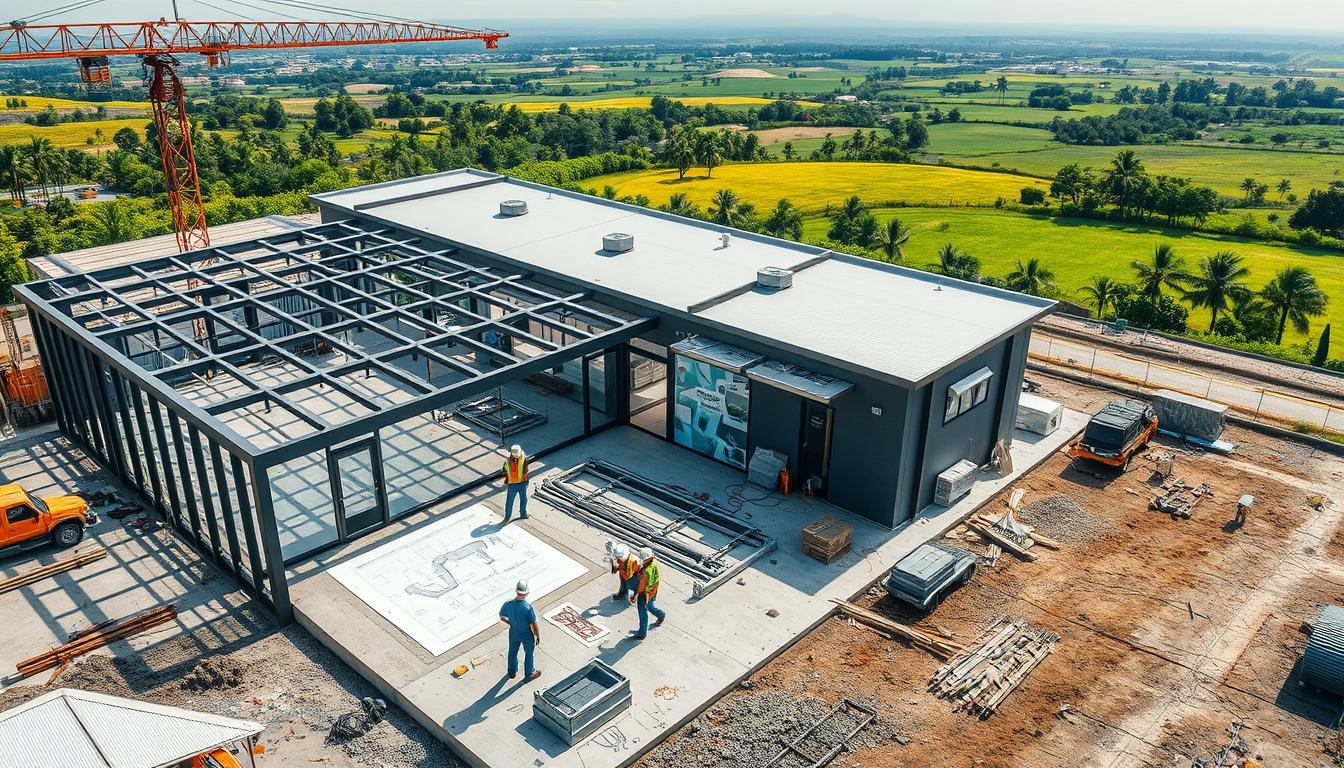
Are traditional construction methods draining your budget and timeline? What if there was a revolutionary approach that could transform your building project’s efficiency and cost-effectiveness?
Pre-Engineered Buildings (PEB) are changing the construction game. They offer big advantages for businesses looking to build smart. In India, the cost of PEB buildings is between ₹200 to ₹600 per square foot. This makes them a great choice for industrial and commercial projects.
PEB structures are incredibly efficient. They can cut construction time by up to 50% compared to old methods. They use advanced engineering to build faster, waste less material, and save money in many areas.
Using PEB technologies changes how we build. It gives us customizable, strong, and green buildings that meet today’s needs. Businesses can get top-notch structures without spending too much upfront. They also save money over time.
Key Takeaways
- PEB building cost ranges between ₹200-₹600 per square foot
- Reduces construction time by 50% compared to traditional methods
- Enables customizable design solutions for diverse industries
- Provides substantial long-term cost savings
- Supports sustainability through efficient material usage
- Offers superior durability and low maintenance requirements
- Applicable across multiple project types including warehouses and factories
Understanding Pre-Engineered Building Systems
Pre-engineered building (PEB) systems are changing the way we build. They make construction faster and more flexible for warehouses and commercial buildings. These systems use new designs to make buildings strong yet light, changing how we build.
- 30-35% lighter than traditional steel buildings
- Superior strength and durability
- Rapid construction timelines
- Versatile application across multiple sectors
Key Components of PEB Structures
PEB warehouses have key parts like primary steel frames and secondary structures. These parts work together to make a strong and efficient building.
Manufacturing Process Overview
PEB manufacturing uses advanced computer designs and automated steel making. This method ensures quality and saves materials. It can cut construction costs by 10-20% compared to old methods.
Design Principles and Standards
PEB design aims to be strong and use less material. Engineering expertise is key to making buildings that meet tough performance standards. This is important for many industrial uses.
PEB systems bring new technology and engineering to construction. They offer cost-effective, sustainable, and flexible solutions for businesses around the world.
Market Trends and Growth Analysis in PEB Industry
The pre-engineered building (PEB) industry is growing fast. This is thanks to new construction methods and a need for cheaper buildings. Experts say there are big chances for saving money in PEB building costs in many areas.
Important insights show the industry is doing well:
- Global PEB market expected to reach USD 16.92 billion in 2024
- Projected CAGR of 11.6% from 2025 to 2030
- Industrial buildings segment dominating with 57.7% revenue share
Portable cabins are getting more popular, mainly for work and business. The Asia Pacific area is growing fast, with a 13.0% growth rate expected. India is also showing a lot of promise for using PEBs.
Things that help the market grow include:
- Building faster (up to 50% quicker than old ways)
- Building cheaper in controlled places
- More money going into building new things
The market looks set to keep getting better. PEBs are changing how we build today.
Cost-Effective Construction Solutions with PEB
Pre-engineered buildings (PEBs) are changing the way we build. They offer big savings and are very efficient. Companies looking for smart building solutions are choosing PEBs. This choice cuts down project costs a lot.
Looking into PEB solutions shows big wins for businesses. These new buildings save money in many ways. They bring economic benefits to companies.
Initial Investment Considerations
When thinking about PEB construction costs, there are important money matters to consider:
- Less money spent on materials than traditional building
- Lower labor costs because parts are made before arriving
- Projects finish faster
- Less need for construction on-site
Long-term Financial Benefits
PEB technology in modern container offices brings long-term savings. The quick build process means quick and lasting money savings:
- Up to 30% less in total project costs
- Less money spent on upkeep
- Better energy use
- Lower running costs
ROI Assessment Factors
Figuring out the return on investment for PEB projects involves looking at several important factors. Key performance indicators include fast build times, less waste, and strong structures.
Companies can see big financial gains. Most PEB projects save 20-30% compared to traditional building. The use of factory-made parts means better use of resources and quality.
PEB Building Cost: Analysis and Breakdown
Understanding the cost of Pre-Engineered Buildings (PEB) is key. The cost varies a lot, with industrial sheds costing between INR 1,500 to INR 2,500 per square foot.
Several factors affect the cost of a PEB structure per square foot. These include:
- Steel materials (60-70% of total project cost)
- Foundation and site work (10-15% of budget)
- Installation and labor expenses (10-15% of total investment)
- Design and engineering services (5-10% of project expenses)
Technologies like Computer-Aided Design (CAD) and Building Information Modeling (BIM) are vital. They help design better and save money. These tools can reduce costs by up to 30% compared to traditional building methods.
PEB structures offer more than just cost savings. They are built faster, often in 6-8 weeks. This saves time and labor. With over 1,000 companies in India focused on PEB systems, finding affordable options is easy.
Managing PEB building costs requires careful planning. Consider the following:
- Selecting the right steel grades
- Optimizing design complexity
- Using local materials
- Reducing transportation costs
By examining these factors, businesses can make the most of pre-engineered building technology. This leads to long-term financial gains.
Material Quality and Selection Impact
The success of PEB structures depends a lot on the quality and choice of materials. High-performance steel is key for making strong and lasting porta cabins for industries. It ensures the structure stays strong and reliable over time.
To understand material performance, we need to know about steel grades and quality control. Choosing the right materials can greatly affect a project’s durability and cost.
Steel Grade Options
There are different industrial-grade steel grades with different performance levels:
- E250 Grade: A budget-friendly choice for basic needs
- E350 Grade: Better strength for tough environments
- High-tensile steel: Best for carrying heavy loads
Quality Control Standards
Strict quality control makes sure PEB structures meet global standards like IS2062 and ASTM572. These standards ensure:
- Consistent material quality
- Strong structure
- Long-lasting durability
Material Performance Metrics
Choosing materials affects how well a structure performs. Higher-grade steel might cost more, up to 20%, but it offers long-term benefits for industries.
Important metrics include strength, resistance to corrosion, and how well it adapts to the environment. Spending on top-quality materials means less maintenance and a longer structure life.
Industrial Applications and Warehouse Solutions
Pre-engineered buildings (PEB) are changing the game in India’s industrial world. They are making a big splash in warehouses and manufacturing. These buildings are flexible and cost-effective, helping businesses thrive.
PEB warehouses are top picks for today’s industrial needs. They offer big advantages like quick builds and lots of storage. Plus, they can grow with your business.
- Rapid construction timelines
- High storage capacity
- Scalable architectural layouts
- Accommodating heavy machinery workflows
PEB warehouses are great for many industries. They’re used in manufacturing, logistics, and even cold storage. Efficient labor colony solutions make these buildings perfect for managing workers.
The cost of PEB warehouses varies from ₹295 to ₹1,25,000 per square foot. Prices depend on height, design complexity, and extra features like insulation.
PEB technology is leading the way in industrial construction in India. It allows for strong, flexible spaces that meet today’s needs. From simple steel frames to full manufacturing setups, PEB is the future.
Labor and Installation Cost Optimization
Pre-engineered building (PEB) solutions are changing construction by cutting labor and installation costs. This new method makes building faster and cheaper. It’s a big win for project managers and developers.
PEB focuses on managing workers and making installation smoother. Using pre-made parts, companies save a lot of time and money.
Workforce Requirements
PEB needs a small, skilled team. Projects require:
- Fewer workers than traditional building
- Technicians for precise assembly
- Less manual work
Installation Timeline Management
Planning installation can shorten building time by 50%. Important steps include:
- Making structural parts ahead of time
- Using modular designs
- High-precision manufacturing
Cost Reduction Strategies
Targeted methods can lower PEB construction costs. Advanced planning and standardized processes are key to efficiency.
- Use standard building parts
- Improve logistics and transport
- Use fast assembly methods
Adopting these new strategies can change how businesses build. It saves money without sacrificing quality.
Foundation and Site Preparation Expenses
Foundation and site preparation are key in figuring out the cost of a PEB building. These steps usually take up 10-15% of the total budget. They are very important for developers and project managers to think about.
Several things affect the cost of foundation and site preparation in pre-engineered buildings:
- Soil bearing capacity
- Ground water levels
- Topographical variations
- Structural load requirements
Doing a detailed site analysis is vital to manage the cost of a PEB structure per square foot. Soil tests help find the best and cheapest foundation options. Engineers must check the ground well to make sure the structure is strong and to save on future costs.
Site preparation activities that add to the cost include:
- Excavation
- Land clearing
- Ground leveling
- Drainage system installation
Planning the foundation well can cut down on long-term construction costs. By doing a good site evaluation and choosing the right foundation, project managers can save money now and in the future.
Using advanced geotechnical tests and precise engineering can lower unexpected site preparation costs. This makes budgeting for pre-engineered buildings more accurate.
Environmental Benefits and Sustainability Features
Pre-Engineered Building (PEB) structures are changing the game in sustainable construction. They offer businesses a chance to build eco-friendly spaces that are both efficient and responsible. This is a big win for the planet and for business goals.
Energy Efficiency Aspects
PEB structures save a lot of energy, cutting costs by 20-40%. They have special features that help:
- Advanced thermal insulation systems
- Integrated renewable energy compatibility
- Optimized structural design reducing heat transfer
Waste Reduction Methods
Steel, the main material in PEB structures, is very sustainable. It can be recycled up to 90% of the time. This means big savings for the environment. The way these buildings are made also helps:
- Precise component fabrication
- Minimal on-site material waste
- Reduced construction debris
Green Building Certifications
Container cafes can use PEB structures to get green building certifications. These designs help businesses create spaces that are good for the planet. It shows they care about the environment.
Using PEB structures can cut greenhouse gas emissions by up to 60%. This shows a real commitment to being green and innovative.
Design Customization and Cost Implications
Pre-engineered buildings (PEBs) let businesses create unique solutions. They can meet specific needs and look great. The cost of a PEB can change a lot, depending on how customized it is. Making smart design choices is key for keeping costs down.
Customization options for modern container office designs include:
- Flexible interior layouts
- Varied roof styles and configurations
- Customizable wall systems
- Adaptable building dimensions
- Specialized architectural features
When thinking about design customization, it’s important to consider the costs. Standard designs cost $10 to $25 per square foot. But, more complex designs can raise engineering and fabrication costs. In India, PEB building costs are between Rs. 300 to Rs. 600 per square foot, based on design complexity.
Key cost factors for design customization include:
- Engineering complexity (5-10% of project cost)
- Material selection
- Structural modifications
- Additional architectural elements
To manage customization costs, businesses can take a few steps. They can balance looks with function, choose standard parts when they can, and focus on the most important design elements. This way, they can save money without sacrificing quality.
Maintenance and Long-term Cost Considerations
Pre-engineered buildings (PEB) are a smart choice for industries looking for strong and affordable solutions. These buildings last long and need little upkeep.
Preventive Maintenance Schedule
Starting with a proactive maintenance plan helps PEB structures last longer. Important steps include:
- Annual checks on the structure’s health
- Keeping the surface coated and protected from rust
- Examining connections and the structure’s strength
- Keeping the weather out and seals in good shape
Lifecycle Cost Analysis
PEB structures save a lot of money over time. They can cut down on maintenance costs by up to 40%. With the right care, they can last over 30 years.
Durability Factors
Key things that make PEB structures durable are:
- Corrosion resistance thanks to special steel treatments
- Being strong against the weather
- Little to no wear and tear
- Being fire-resistant
Companies can save a lot by choosing PEB structures. They save on maintenance, energy, and extend the life of their buildings.
Regional Cost Variations and Market Factors
The pre-engineered building (PEB) market shows big differences in cost across regions. In India, the cost of PEB buildings is between Rs. 300 to Rs. 600 per square foot. This cost is affected by many economic factors.
The Asia Pacific region, like India and China, is growing fast. This growth is because of quick urbanization and more infrastructure projects.
How much a PEB costs per square foot varies by region. North America is a big player, while countries like India are growing fast. Companies like Tata BlueScope Steel and Kirby Building Systems are leading the way with new solutions.
Steel is a big part of the PEB market, making up about 35% of its revenue. This shows how important steel is in calculating costs.
Prices change a lot because of economic conditions, local materials, and labor costs. In India, the PEB market is expected to grow a lot. It will go from USD 0.501 billion in 2024 to USD 0.888 billion by 2032, growing 7.40% each year.
Companies are now investing in technology and making products closer to where they are used. Over 1,000 companies in India offer prefabricated structures. This is making the market better and more affordable for different needs.
FAQ
What are Pre-Engineered Buildings (PEBs) and why are they becoming popular?
Pre-Engineered Buildings are new ways to build that save money and time. They are 30-35% lighter than regular steel buildings. This makes them stronger and more durable, cutting down on construction costs and time.
How much do PEB structures typically cost?
PEB buildings usually cost between and per square foot. In India, prices range from INR 1,500 to INR 2,500 per square foot. The price depends on the size, complexity, and specific needs of the building.
What industries can benefit from PEB construction?
PEB structures work well for many industries. They are great for warehouses, manufacturing, logistics, cold storage, and more. They offer flexible designs for different needs.
How do PEBs contribute to sustainability?
PEB structures can save 20-40% on energy costs over time. They use steel, which is mostly recyclable. This makes them a green choice for building.
What are the key advantages of choosing PEB over traditional construction?
PEB structures are cheaper by 20-30% and faster to build by up to 50%. They also cost less to maintain and are more energy-efficient. Plus, they offer more design options.
How long do PEB structures typically last?
With good care, PEB structures can last over 30 years. Their strong design and quality materials ensure they stand up to different weather conditions.
What steel grades are typically used in PEB construction?
PEB buildings often use E250 and E350 steel grades. These meet international standards like IS2062 and ASTM572. Higher-grade steel costs more but is stronger and lasts longer.
Can PEB structures be customized?
Yes, PEB structures can be customized a lot. You can choose different sizes, roof styles, and layouts. While custom designs might cost more, they meet specific needs and looks.
How do PEB construction costs compare across different regions?
PEB costs vary by region due to local material and labor prices. In India, for example, prices are between Rs. 300 to Rs. 600 per square foot, influenced by local market conditions.
Are PEB structures suitable for portable or temporary buildings?
Yes, PEB technology is perfect for portable buildings like offices and temporary facilities. They are quick to set up, cost-effective, and durable for both short-term and long-term use.